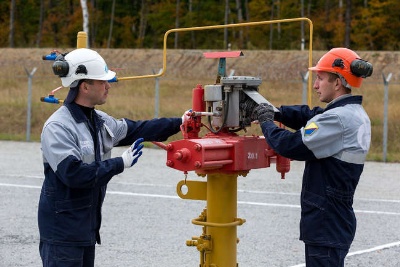 Эта история происходила в первой половине 80-х годов прошлого века. На территории Куйбышевской тогда области. Объединение Куйбышевнефть и завод Тольяттиазот участвовали в инновационном проекте. Одной стороне, нефтяникам, необходимо было повышать отдачу нефтяных месторождений высоковязкой нефти. Другой стороне, химикам, нужно было утилизировать углекислый газ, который был побочным продуктом основного производства. До 1981 года углекислый газ выбрасывался в атмосферу. Но уже тогда, без всяких Гринписов и прочих гринов и писов, правительство и партия заботились об окружающей среде и здоровье нации. В результате появился проект закачки углекислого газа в нефтеносные пласты.
К тому моменту в НГДУ "Сергиевскнефть" эксплуатировалось три основных месторождения: Радаевское, Якушкинское и Козловское. На двух из них (Радаевском и Козловском) и решено было проводить эксперимент:
Радаевское месторождение. Начало освоения - 1948 год. Промышленная добыча велась с 1950 года и к моменту начала проекта многие скважины уже были сильно обводнены.
Козловское месторождение. Промышленная добыча началась позже, чем на Радаевке, с 1965 года.
Основными для добычи были угленосные пласты Б2 с глубиной скважин 1400-1600 метров.
Тольяттиазот. Вот что говорит о нем Википедия: "Строительство завода по выпуску минеральных удобрений (аммиака и карбамида) возле Тольятти началось в 1974 году по договору с американской фирмой «Оксидентал Петролеум». Завод строился с финансовым участием американского миллиардера Арманда Хаммера, питавшего симпатии к СССР и лично знакомого с В. И. Лениным. Строительство было объявлено Всесоюзной ударной комсомольской стройкой. Одновременно с возведением завода для транспортировки аммиака велась прокладка магистрального аммиакопровода «Тольятти-Одесса» протяжённостью более двух тысяч километров. Первая продукция предприятия «Тольяттиазот» была выпущена в 1979 году". О производстве сжиженного СО2 ни слова.
А вот краткое упоминание о проекте на официальном сайте завода: "В апреле 1979 г. «Тольяттиазот» выдал первые тонны аммиака. В том же году был введён в работу первый агрегат по производству карбамида. За ним буквально через полгода последовал пуск второго. В августе 1983 г. получена первая продукция жидкой двуокиси углерода; в октябре 1985 г. сдана в эксплуатацию установка по получению карбамидоформальдегидной смолы (КФС); в июне 1986 г. введён в строй последний, седьмой агрегат аммиака".
В Самарской прессе иногда вспоминают о славной истории Суходольских нефтяников: "НГДУ «Сергиевскнефть» всегда было пионером в плане применения новой техники и современных технологий в нефтедобыче. Месторождения в Сергиевском районе служили полигоном для апробирования метода полимерного заводнения пластов. Именно здесь - впервые в нашей стране – был внедрен метод разработки Боровского месторождения с применением внутрипластового горения в известняках, метод разработки Радаевского и Козловского месторождений с применением закачки в пласт двуокиси углерода, которые, несомненно, являются лучшими достижениями науки в нефтедобыче".
Первоначальный проект предполагал транспортировку газа с завода по трубе и закачку его на месторождениях в газообразном же виде. Трубу планировали проложить в одном створе с продуктопроводом на Одессу. Но в то время по отношению к СССР действовали очередные американские санкции, это привело к кардинальным изменениям в проекте. В стране не было компрессоров способных создать необходимое давление газа. А немецкие партнеры (ФРГ), ведущие работы на заводе Тольяттиазот, отказались поставлять нужное оборудование. Тогда то и было принято решение провести эксперимент по транспортировке с завода и закачке в скважины сниженного углекислого газа . Проект стартовал в мае 1981 года. Курировал его заместитель министра Министерства нефтяной промышленности СССР - Соколов. Начальником проекта был назначен старший инженер ЦПДД Степаненко Г.Ф., который потом и возглавил цех по транспортировке и закачке двуокиси углерода.
В то время промышленность выпускала трубы первого и второго сорта. Причем получить с завода только трубу 1-го сорта было невозможно. В обязательном порядке 10% от поставки было трубы второго сорта. На основную трассу шла труба диаметром 426 мм толщиной 11мм. В оврагах толщина трубы была 12 мм, в поймах и на переходах рек - 16 мм. Через каждые 10-12 км устанавливались распределительные пункты - вагончик с телефонной связью, автоматикой, задвижкой с электроприводом и возможностью дистанционного управления из диспетчерской (на территории завода), такие же пункты строились у переходов через реки. Отвод на Радаевское месторождение был диаметром 325 мм, на Козловское - 219 мм.
Чтобы убедиться в возможности применения труб 2-го сорта, заместителем министра по капитальному строительству было дано указание провести испытание трубы на давление 150 атм. при проектном рабочем давлении 100 атм. Сварили 200 метровый участок в поле, поставили сферические заглушки, пригнали специальный компрессор ЦА 320 и начали закачку воды. Давление увеличивали не спеша, почти два дня потратили. Подходили к трубе тоже аккуратно, старались даже не шуметь. За сутки испытаний давление упало на 2 атмосферы и эксперимент признали удачным.
По территории завода трубу укладывали немецкие специалисты, ну а наши сварщики учились у них и практиковались на заводе 2 недели. А потом, трубу от завода до месторождений укладывали уже своими силами. Строгий контроль всех работ, рентгенография каждого сварного шва - нефтяники учились строить по новым технологиям. Использовали индукционный предварительный нагрев - это уменьшало количество брака. Усложнение работ и дополнительный контроль увеличивали затраты, но делалось это все не просто так. Дело в том, что жидкая углекислота при резком падении давления не переходила в газообразное состояние, а превращалась в сухой лед. Температура -55 по Цельсию и лёд, который в объеме в 6 раз больше чем жидкий СО2 - такой фазовый переход превращал маленькую трещину в огромный разрыв. Подобный эксперимент по закачке жидкой углекислоты на Аляске закончился значительными разрушениями и жертвами.
Я написал что на трубе устанавливались задвижки с электроприводом. Но и задвижки диаметром 400 мм с рабочим давлением до 100 атм. в СССР не производились. В конкурсе на поставку задвижек большого диаметра участвовали ФРГ и Япония. Правда японские задвижки были рассчитаны только на 60 атм. давление. Было принято решение о закупке задвижек в Японии ввиду их меньшей стоимости, а кроме того немецкие изделия попали под санкции. Поэтому на территории завода стояли немецкие задвижки, а на трубопроводе за территорией завода - японские. Давление в трубопроводе было от 90 атм. на заводе до 30 атм. на месторождениях.
Мелкие задвижки на 50, 80 и 100 мм и предохранительные клапаны по специальному заказу изготавливались на одном из Ленинградских оборонных заводов. Для этого начальнику проекта пришлось сначала "пролоббировать" чтобы в проекте была предусмотрена арматура не из обычной Сталь 20, а из нержавейки 15ХА. Отдельно на такие заказы "выбивались лимиты" в министерстве, были и поездки на заводы, для которых эти заказы были не только сверхплановыми, но и, как модно сейчас говорить, инновационными. В Баку изготавливали клапаны и фонтанную арматуру, в Волгограде блок-боксы. Промышленность СССР получила возможность развития благодаря американским санкциям, так же как теперь промышленность России осваивает новые технологии и новую номенклатуру изделий.
Для закачки жидкого СО2 в скважины давление на устье нужно было поднять до 110-120 атм. Но мы же помним, что американские санкции уже действовали и поставку специальных компрессорных станций на проект "партнеры" заблокировали. Но и тут нашлось у русских инженеров решение - применили погружные насосы. На промыслах в специальные шурфы вертикально опустили трубы диаметром 500мм и длиной около 50 м. На поверхности был 6-ти дюймовый вход из трубопровода, а на глубине 10 м 4-х дюймовый выход на скважины. Насос опускали на 20-ти метровую глубину. Вот так смекалка и знакомые в эксплуатации погружные центробежные насосы позволили начать закачку СО2 в пласт. Корпуса и валы ЭЦН также по специальному заказу изготавливались из нержавеющей стали.
9 апреля 1982 года в НГДУ "Сергиевскнефть" начал работать новый цех по транспортировке и закачке двуокиси углерода. Сначала запустили 5 скважин на Радаевке. Потом количество скважин постепенно увеличили, а в 1983 году запустили закачку и на Козловке. Закачивали в скважины поочередно 2 недели воду, потом 2 недели СО2.
Не все шло гладко, практически каждый месяц случались аварии на трубопроводе. К счастью на производстве смертельных случаев не было. При авариях и просто в дежурном порядке на вертолетах совершали облет трассы.
При порывах трубы выходящий углекислый газ приводил к гибели урожая на полях примерно на одном гектаре. Летом дым от горящего стога соломы можно было легко принять за порыв трубопровода - интенсивное испарение СО2 сопровождалось густым белым шлейфом. Вот при одном порыве нашелся активист, который проезжая мимо, захотел посмотреть что там горит. И пошел на "дым". На краю воронки видимо ему стало плохо от недостатка кислорода, он упал в неё и замерз, температура то -55 С, даже жарким летом.
Однажды на одной из задвижек обнаружили утечку на сальнике. Выехала бригада. Сняли давление, все наладили. Стали открывать задвижку - не пошла. Снова сняли давление... и так три раза. В результате металл задвижки охладился до тех самых минус 55 и она разлетелась. И хотя в будке никого не было и все манипуляции выполнялись дистанционно, взрывной волной людей отбросило, осколки долетели до трансформаторной подстанции метрах в 50 от распредпункта.
Не смотря на все трудности закачку сжиженного СО2 в пласты вели до 1987 года. Эффект получили значительный, некоторые скважины даже начали фонтанировать. На одной скважине нефть пошла из затрубного пространства.
Изначально проект предусматривал второй этап. Предполагалось очищать попутный газ, который теперь содержал большой процент СО2 и не сгорал в факелах, и закачивать его обратно в пласт. Однако, в этом случае пришлось бы постепенно снижать поступление СО2 с завода. Экономика всего проекта ухудшалась в связи с дополнительными затратами на очистку и компремирование попутного газа. Заводу, в свою очередь, так же не выгодно было снижение объемов поставки. Все это привело к сворачиванию проекта.
В 1987 году постановлением пленума ЦК КПСС проект был закрыт.
|